Engineering researchers at the University of Toronto say they’ve developed the world’s most efficient organic light-emitting diodes (OLEDs) on plastic.
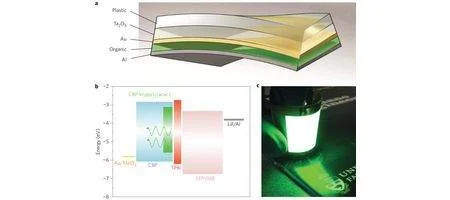
It means an alternative to rigid glass, potentially allowing flexible displays at low cost. The team says its device is comparable with the best glass-based OLEDs, while providing all the benefits of plastic.
Most OLEDs are currently produced using heavy-metal doped glass in order to achieve high efficiency and brightness – but this makes them expensive to manufacture, heavy, rigid and fragile.
“For years, the biggest excitement behind OLED technologies has been the potential to effectively produce them on flexible plastic,” says materials science and engineering professor Zheng-Hong Lu.
“This discovery, unlocks the full potential of OLEDs, leading the way to energy-efficient, flexible and impact-resistant displays.”
Lu and his team were able to match the high refractive index previously only achievable by heavy metal-doped glass by using a 50-100 nanometre thick layer of tantalum(V) oxide (Ta2O5), an advanced optical thin-film coating material.
This advanced coating technique, when applied on flexible plastic, allowed the team to build the highest-efficiency OLED device ever reported with a glass-free design.
OLEDs provide particularly high-contrast and low-energy displays. They are currently used in some cellphones and other small devices, but are starting to be used more widely.
The new technique, and its lower cost, could help them really take off – and could aid the development of bendy screens – although it could be a while before they make it to large-scale manufacturing.